Introduction
From time to time, a company produces a new fiber or fabric that has far-reaching impacts on the activewear industry. Polyester, synthetic fleece, and synthetic insulation are products that dramatically changed how people dress for outdoor activities.
Teijin, a large Japanese textile manufacturer ($8 billion revenue in 2020), introduced Octa fibers in 2018. Octa is used to manufacture Octa Active Mesh. This fabric has been implemented in various products, including the Arc’teryx Proton FL (as well as several other Arc’teryx products), the Noronna Faltikind Octa, the Mountain Equipment Kinesis Insulated Jacket, and now, the Mountain Hardwear AirMesh Shirt and Kor AirShell Warm Jacket.
I wrote briefly about Octa in my article on active insulation. I have also participated in a forum discussion dealing with the Mountain Hardwear AirMesh.
In this article, I will comprehensively review Octa as implemented in Mountain Hardwear AirMesh garments. This article includes extensive lab testing and limited field testing while hiking, biking, and running. When we refer to AirMesh in this article, it will be in reference to the fabric used in the Mountain Hardwear garment.
I discuss the fundamentals of base layer wicking and drying and the test methods used in this article in detail in two prior articles (here and here). I recommend reading those articles to better understand the concepts and techniques discussed here.
Editor’s Note: For the sake of clarity, we’ve added links in context throughout the article to other installments of Stephen Seeber’s work (as we did above). In addition, we recommend readers spend some time catching up on all of Stephen Seeber’s By the Numbers series. It is a body of work that builds upon itself, and readers will find a complete exploration of the series time well spent.
Summary of results
Briefly, here is what I have found about the Mountain Hardwear AirMesh shirt:
- My Wick/Dry test revealed that wetting performance and, therefore, wicking of AirMesh is limited by the brushed skin-side surface of the fabric.
- The restricted capillary capacity of the very lightweight fabric also limits wicking performance – there are insufficient capillaries to transport much moisture without reaching saturation.
- Air permeability of the fabric is high but quite a bit lower than that of 60 gsm (grams per square meter) Alpha Direct. This air permeability will promote dumping excessive heat through convection when sufficient ventilation is provided.
- AirMesh’s warmth is good for such a light fabric, but 60 gsm Alpha Direct surpasses the warmth-to-weight performance of AirMesh fabric.
- The impressive warmth relative to other wicking base layer fabrics of similar weight results from the Octa fiber structure, which traps more air per fiber than a standard cylindrical polyester fiber.
- The drawback of this fiber structure is that when saturated, it will trap and hold more moisture than similar weight fabrics constructed of conventional polyester fiber. This means that if you saturate this fabric, it will dry slowly and when wet, suffer from degraded thermal performance.
- In drying tests from saturation, the fabric dries at a considerably slower rate than 60 gsm Alpha Direct and an equivalent rate to 100 gsm conventional wicking fabric.
How is AirMesh constructed?
AirMesh is 100% polyester knitted from Teijin Octa fiber. Octa fiber is shown in Figure 1. A knit image is shown in figure 2.
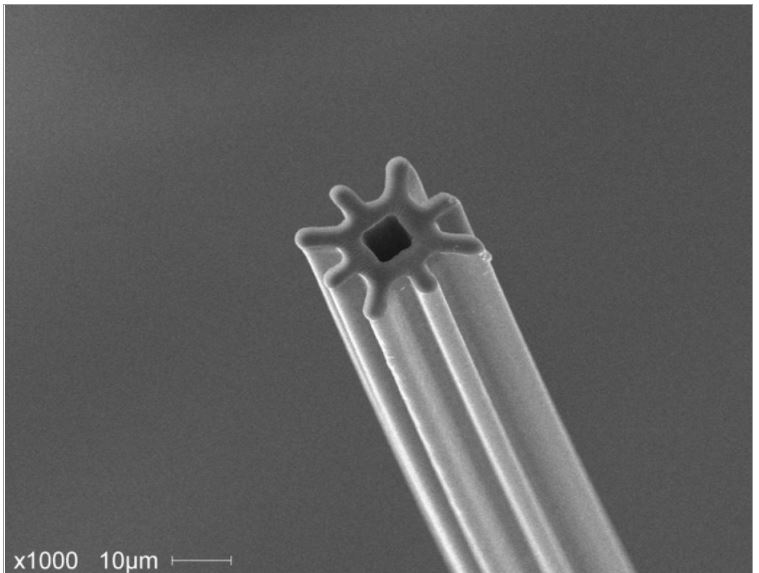
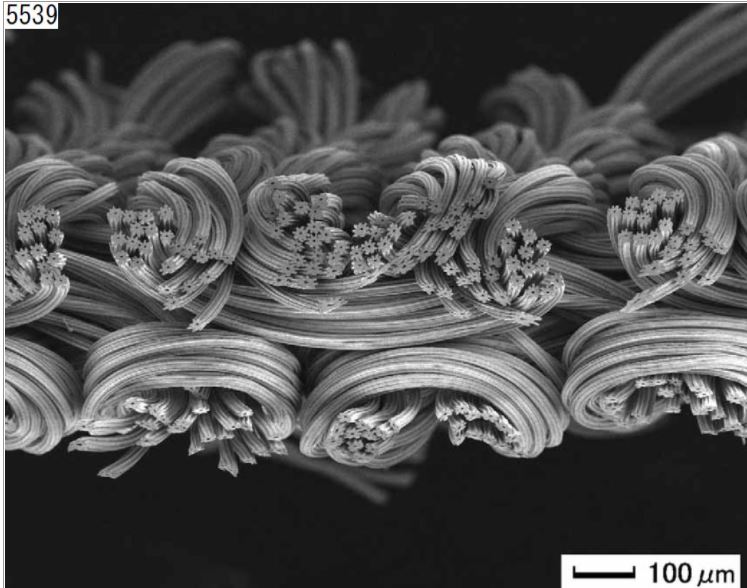
Instead of a typical (i.e., cylindrical) polyester fiber or even a more complex polyester fiber like Coolmax (i.e., an oblong bi-lobal cross-section), Octa has a square hollow core and eight lobes that project from a square fiber extrusion. The hollow core and projecting lobes trap more air than other polyester fiber designs. The fiber construction also provides substantial loft to a very lightweight fabric. As a result, the fabric feels surprisingly light and surprisingly warm when handled.
Figures 3 and 4 show the face and skin side of an AirMesh fabric at low magnification. Figure 3 is backlit, figure 4 is not.
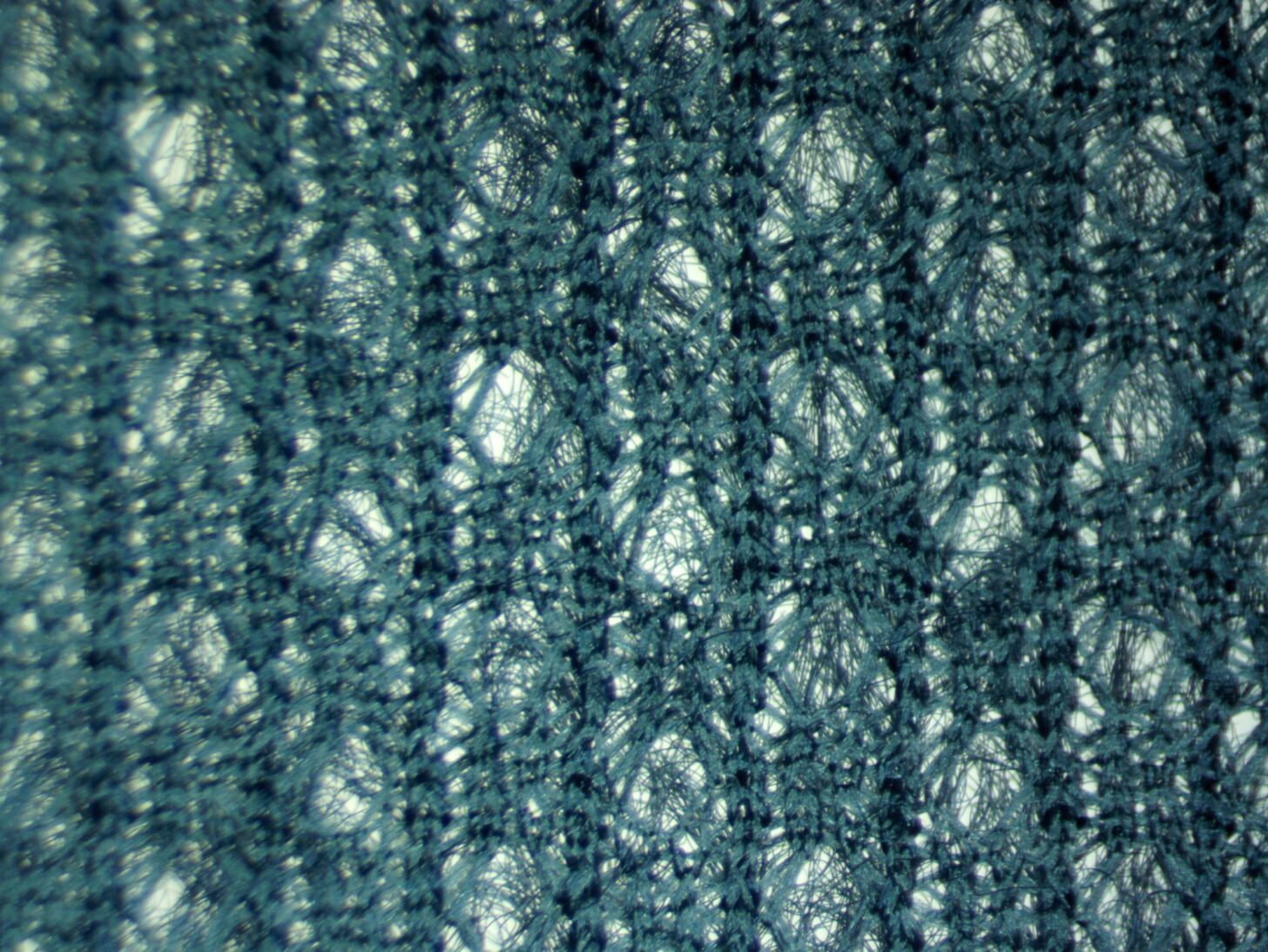

The face side of the fabric is a very loose knit with a grid of holes for increased air permeability. The skin side is lightly brushed, providing additional loft.
As can be seen from the Figure 3 face-side image, the knit is very porous. In the backlit white areas, the brushed fibers on the skin side block some of the light from coming through. Figure 4 shows the brushed fibers on the skin side – these function similarly to napping on fleece.
Summary laboratory test results
Table 1 presents a summary of laboratory test results.
Table 1: Summary laboratory test results
AirMesh | 60 GSM Alpha Direct | 100 GSM Wicking Fabric | |
---|---|---|---|
Weight GSM Fabric | 83 | 60 | 100 |
Weight OSY Fabric | 2.45 | 2.42 | 2.95 |
Porosity (%) | 14 | 27 | 10 |
Air Permeability | 740 | 920 | 500 |
Shirt Weight (grams) for Airmesh and 60 gsm, both pullover, estimated weight for 100 gsm fabric | 117 | 106 | 150 |
Approximate thickness (inches) | 0.076 | 0.1 | 0.025 |
R-value | 0.35 | 0.39 | 0.08 |
R-value/grams per square meter | 0.0042 | 0.0065 | 0.0008 |
Spin Dry Water Weight Gain (% Dry Weight) | 52% | 26% | 31% |
Saturation Test Sample Weight (grams) | 38 | 37 | 36 |
Saturation Test Sample Water Weight Gain (grams) | 96 | 92 | 67 |
Saturation Test Dry Time (minutes) | 68.3 | 39.08 | 52.83 |
Saturation Test Drying Rate (grams/minute) | 1.24 | 1.87 | 1.26 |
Wick/Dry Test Results: Wicking (grams) | 6 | NA | 25 |
Wick/Dry Test Results: Infab (grams) | 1.5 | NA | 11 |
Wick/Dry Test Results: Evap (grams) | 4.5 | NA | 14 |
Wick/Dry Test Drying Time (minutes) | 6.58 | NA | 21.8 |
Wick/Dry Test Drying Rate (grams/minute) | 1.46 | NA | 1.56 |
The laboratory testing provides data for AirMesh, 60 gsm Alpha Direct and a 100 gsm knit wicking fabric. I selected 60 gsm Alpha Direct to include in the comparison because it seems like a logical competitor to Airmesh: it is extremely light, very porous, and has a high warmth-to-weight ratio. The 100 gsm wicking fabric is a typical polyester knit. Although a little heavier than the other two fabrics, it is strikingly thin compared to the other two fabrics.
It is useful to compare similar weight fabrics as we look at performance. We can see that AirMesh falls between the two other fabrics. In the range of wicking fabric weights, these are all on the low end. The comparison for thickness shows a distinct difference between the 100 gsm “typical” wicking fabric and AirMesh and Alpha Direct. The AirMesh and Alpha Direct fabrics are both brushed, increasing the fabric’s thickness. Thickness increases various performance characteristics, of which warmth is the most notable.
Discussion of test results
Air permeability
Alpha Direct has the highest air permeability of the three fabrics, followed by AirMesh and the 100 gsm fabric.
Thermal performance
I measured R-value performance for the three fabrics on my guarded hot plate. We can see that Alpha Direct is a bit warmer than AirMesh. The 100 gsm fabric comes in a distant third to Airmesh and Alpha Direct. The differences between AirMesh and Alpha Direct become more significant when viewed in terms of warmth/weight. The Alpha Direct fabric is 28% lighter than AirMesh and 10% warmer. On a warmth-to-weight basis, Alpha Direct outperforms AirMesh by almost 155%.
Water absorption/drying tests
I hypothesized that the favorable warmth-to-weight performance of AirMesh would also contribute to increased levels of trapped moisture in the fabric when drying conditions were adverse. I did a series of tests to demonstrate whether this might be correct and, if so, how the performance compares with other fabrics.
A simple, non-standard test I performed was a rinse/spin dry test in the washing machine. This test saturates the test samples during the rinse cycle and then attempts to extract water in the spin cycle. In principle, the fabric with the highest hydrophilicity and highest pore volume will retain the most water. I expected this fabric to dry the slowest when saturation occurs during field use. We can see from the data that AirMesh retained substantially more water than either Alpha Direct or the 100 gsm wicking fabric.
Next, I performed a saturation test. In this test, I submerged each sample in warm water and then compressed the sample to remove excess moisture. I weighed each sample to determine how much water was absorbed into the fabric. I performed this process five times and averaged the results. Again, I expected the fabric with the highest hydrophilicity and/or highest pore volume to retain the most water. I also expected this fabric to dry the slowest when saturation occurred during field use. We can see from the data that AirMesh again retained the most water, followed closely by Alpha Direct, with the 100 gsm wicking fabric retaining the least moisture.
Finally, I soaked each test fabric to achieve the average water content produced by the above saturation test. I then placed each test fabric on the permeation kettles to dry. A thermal imager monitored the drying process. As the drying process begins, surface temperatures on the kettles will be low due to evaporative cooling. The temperatures will rise as drying occurs and then stabilize over the entire surface once drying is complete. The data from the thermal imager allows us to observe and time this process and then calculate the total drying time and drying rate (grams of water/minute) for each test fabric.
The dry time for the 100 gsm fabric is 77% of the dry time for AirMesh. This difference corresponds closely to the difference in absorbed water weight between the two fabrics. The rate of drying for the two fabrics is nearly identical. These outcomes are consistent with the findings in my last article about these issues.
The drying time for Alpha Direct is 57% of the dry time for AirMesh. It dries in just over half the time! Why is this? There are two possible reasons:
- Alpha Direct is hydrophobic, and AirMesh is hydrophilic. As a result, the cohesive force between water and fiber for AirMesh is stronger than the cohesive force between water and fiber for Alpha Direct. This difference in cohesive forces means that evaporation of water from Alpha Direct should require less energy than does AirMesh. For nearly any given temperature/humidity combination, Alpha Direct will dry faster than AirMesh. For a further explanation of the concepts behind this statement, see my first base layer article.
- The yarns and fibers for Alpha Direct have more surface area exposed to air than Airmesh.
I suspect reason #1 is more likely here. I intend to do further testing to verify the impact of hydrophilicity vs. hydrophobicity on drying. I will write about the results in a future article.
Figure 5 shows plots of the drying times. The boxes associated with each plot show the drying time and the average surface temperature when fabrics achieve dryness.
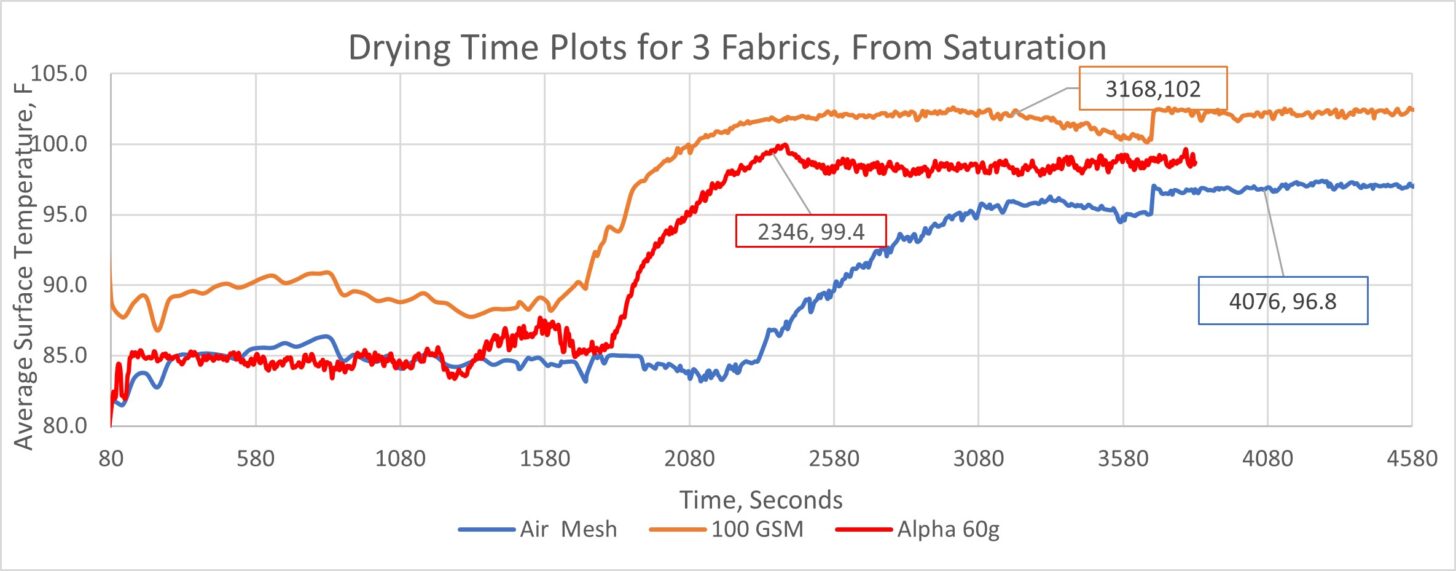
The video below shows the drying progress for Alpha Direct 60g and Airmesh. I provided a timestamp at the bottom of the image. As can be seen, Alpha Direct is nearly fully dry as Airmesh begins to visibly dry.
Wicking performance
I performed my Wick/Dry test on AirMesh and the 100 gsm wicking fabric. Since Alpha Direct is hydrophobic, I did not perform a wicking test on that fabric.
You can read more about how I perform the Wick/Dry test here and here.
The Wick/Dry test demonstrated poor wicking for AirMesh compared to the 100 gsm fabric. We see in Table 1 that the 100 gsm wicking fabric wicked over four times as much moisture as AirMesh. The moisture remaining in the 100 gsm fabric was over seven times greater than in the AirMesh. The amount of moisture that evaporated from the 100 gsm fabric was over three times greater than for the AirMesh.
The test probably overstates the amount of moisture that wicked into AirMesh. The measured wicking quantity is so low that a substantial portion of the water that left the sponge would probably result from the evaporation of water from the sponge. The released water vapor then passed directly through the AirMesh fabric. The water vapor did not contribute to the spread of moisture in AirMesh or the moisture remaining in the fabric at the end of the test.
We can better understand the poor wicking performance of AirMesh by watching the video below.
The video shows the AirMesh on the left and the 100 gsm fabric on the right. As the video progresses, the wicking presents as cold surface temperatures that spread from the sponge (the water source), located at the center, below each test fabric. In the AirMesh, the moisture spreads a limited distance and then stops. Moisture in the 100 gsm fabric spreads over nearly the entire surface of the right kettle. AirMesh’s poor wicking performance is happening for two reasons:
- Low capillary capacity. Low capillary capacity is present in AirMesh due to relatively few yarns per square inch and a large portion of void space between the yarns (see Figure 3 above).
- Poor wetting performance. Poor wetting performance in AirMesh results from the presence of brushed fibers that extend from the skin side. My first article on wicking concluded that napped or brushed fibers require extra force to start the wetting process and as a result, napped or brushed surfaces cannot provide reliable wicking performance.
We can see the impact of the brushed skin side in the following video. In this video, the left image is face-side up, so the skin-side brushed fibers contact the sponge. The right video is skin side up, so the knit face fabric fibers contact the sponge. On the left image, the moisture spread covers less surface (60 cm2) than we see on the right image (86 cm2). Here is how they compare:
The impact of the brushed skin side is seen in the following video. In this video, the left image is face-side up (“Face-Up”), so the skin-side brushed fibers contact the sponge. The right video is skin side up (“Skin-Up”), so the knit face fabric fibers contact the sponge. On the left image, the moisture spread covers less surface (60 cm2) than we see on the right image (86 cm2). Here is how they compare:
- The Face-Up test wicked half the moisture of the Skin-Up test.
- The Face-Up test had 1/3 the moisture in the fabric at the end as the Skin-Up test.
- The Face-Up test evaporated half the moisture of the Skin-Up test.
In comparison, the 100 gsm fabric demonstrates substantially better wicking and drying performance than either the Face-Up or the Skin-Up tests. Here are comparisons with the Skin-Up test results.
- The 100 gsm fabric wicked more than twice the moisture as the Skin-Up test.
- The 100 gsm fabric had nearly four times as much moisture in the fabric at the end of the test as the Skin-Up test.
- The 100 gsm fabric evaporated nearly twice as much moisture as the Skin-Up test.
After completing the Wick/Dry test, I weighed the AirMesh and 100 gsm fabrics and set them on the kettle surfaces to dry, with the thermal imaging measuring the drying time and drying rate.
As expected, the drying rates were close for the two fabrics, but the 100 gsm fabric took far longer to dry because it held more than seven times more water than the Airmesh fabric.
Field test results
I wore the AirMesh shirt for a 5-mile (8 km) run and a 20-mile (32 km) bike ride. For the run, I wore the AirMesh beneath a Patagonia Houdini wind shirt. The AirMesh was my only layer on the bicycle ride. The shirt retained 57 grams of moisture after the run, with another 106 grams of moisture condensed on the inner surface or the weave interstices of the wind shirt. After the bicycle ride, the AirMesh retained 23 grams of moisture, despite constant airflow over the shirt.
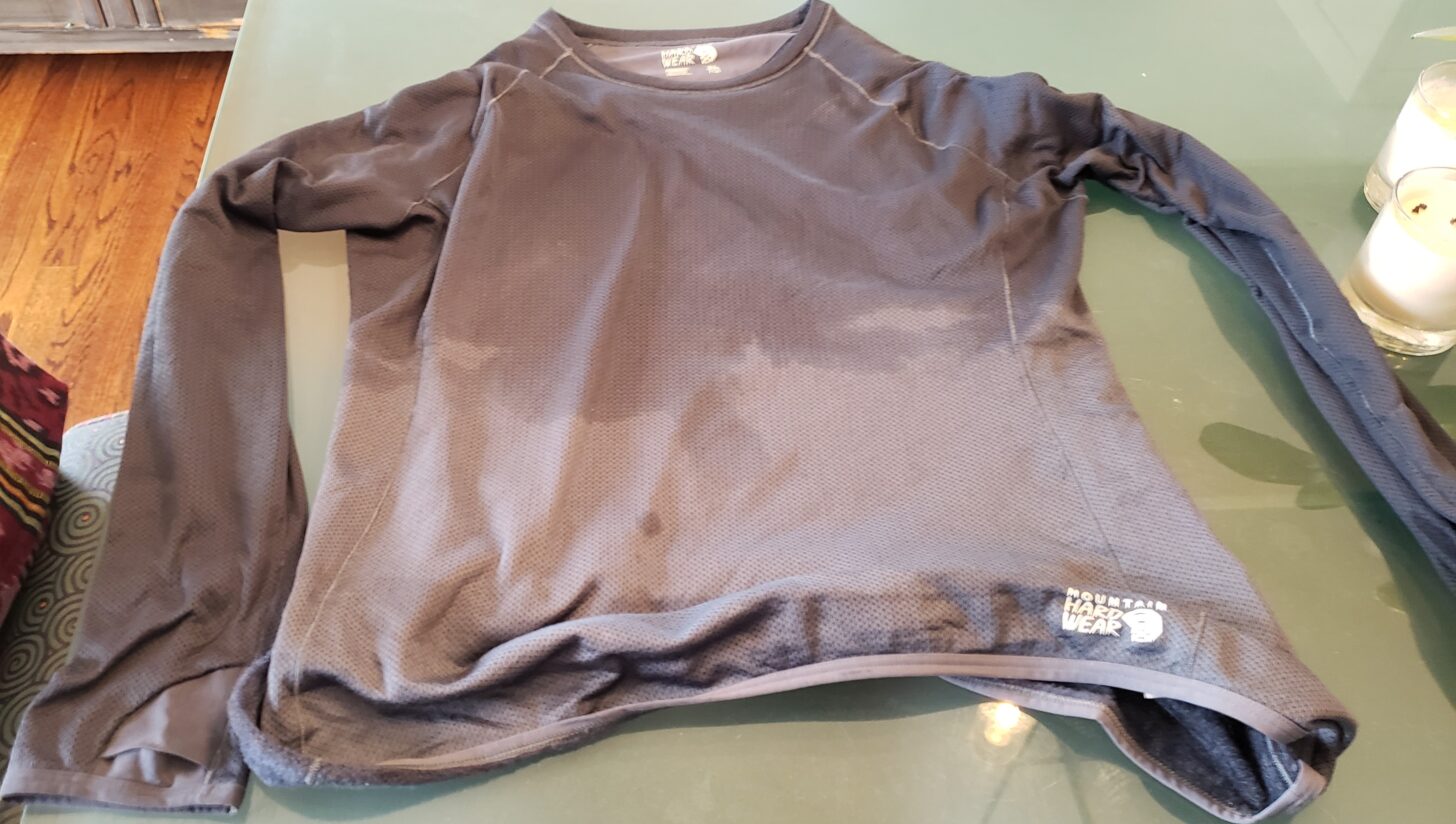
Figure 6 shows absorbed moisture on the chest and sleeves of the shirt. The same pattern repeats on the back. From this photograph, I suggest the following:
- We can conclude that wicking and drying were not keeping up with sweat generation during the run.
- Moisture did not effectively spread into dry portions of the shirt.
- Effective wicking appears to have occurred only where the shirt was under sufficient pressure to support wetting. This pressure happened at the chest, upper back, and sleeves.
Wicking did not happen on the lower portions of the shirt. These areas were generally dry. Moisture transfer in these areas would be limited to whatever could evaporate on the skin and travel through the fabric. The wind blew during the run, which should have maintained some pressure on the lower portions of the shirt. Evidently, there was not enough pressure to encourage wicking. Of course, as is often the case with field tests, we can only speculate on the causes of the wetting pattern seen here.
We do know that at saturation, the Airmesh fabric can absorb about 2.5 times its fabric weight in water. Let’s assume that the shirt above is 2/3 wet. Let’s assume that piping, stitching, and labels account for 15% of the shirt weight. That means this shirt, when saturated as shown in the photograph, would accumulate an extra 67 grams. This weight is fairly close to the 57 extra grams of water weight we measured in this shirt. It is likely that most of the areas that appear wet in this shirt are saturated and that the wicking ability of the fabric was degraded after the one-hour run.
Conclusions
Our testing revealed that the Airmesh fabric does provide very good warmth to weight performance. However, Alpha Direct 60 gsm provides greater warmth and a substantially better warmth-to-weight performance.
The tests also confirmed that Airmesh can absorb more water than the conventional wicking fabric or Alpha Direct. Elevated moisture absorption can substantially degrade the good thermal performance produced by the Airmesh shirt when dry. Our drying tests showed that drying performance of saturated Alpha Direct was far superior to Airmesh.
Our wicking/drying test reveals that Airmesh offers inferior wicking performance compared to a conventional wicking fabric due to unreliable wetting performance and limited capillary capacity.
Field tests suggest that moderate to high exertion levels can get this shirt to approach saturation conditions quickly.
The test results presented here should give the readers a pretty good idea of what to expect from the Airmesh shirt for their intended uses. As a result, the readers can make an informed decision as to whether or not this garment is likely to meet their needs and improve on performance available from other options. In my opinion, I would avoid the AirMesh shirt for high output activities where elevated sweat will be produced and ventilation to help drying is limited.
Learn more
Browse our curated recommendations in the Backpacking Light Gear Shop – a product research & discovery tool where you can find Member gear reviews, Gear Swap (used gear) listings, and more info about specific products recommended by our staff and members.
Gear Shop » Clothing Systems
Related content
- Catch up on the rest of the By the Numbers series.
- Explore the rest of our Gear Testing and Research content.
- Read our community’s discussion of Mountain Hardwear AirMesh garments in this forum thread.
DISCLOSURE (Updated April 9, 2024)
- Product mentions in this article are made by the author with no compensation in return. In addition, Backpacking Light does not accept compensation or donated/discounted products in exchange for product mentions or placements in editorial coverage. Some (but not all) of the links in this review may be affiliate links. If you click on one of these links and visit one of our affiliate partners (usually a retailer site), and subsequently place an order with that retailer, we receive a commission on your entire order, which varies between 3% and 15% of the purchase price. Affiliate commissions represent less than 15% of Backpacking Light's gross revenue. More than 70% of our revenue comes from Membership Fees. So if you'd really like to support our work, don't buy gear you don't need - support our consumer advocacy work and become a Member instead. Learn more about affiliate commissions, influencer marketing, and our consumer advocacy work by reading our article Stop wasting money on gear.
Home › Forums › By The Numbers: Testing the Performance of Mountain Hardwear AirMesh Garments